Solving DC/DC Conversion for OEM’s
One critical piece of technology for a vehicle manufacturer is the conversion of power within their system. Since virtually all systems on mobile equipment is direct current (DC) , the challenge of power conversion is typically the DC to DC portion.
Most electrical components on board mobile vehicles were in some fashion developed out of the automotive industry and adapted for use in off-highway. This means they are typically 12vdc. But unlike automotive, the off-highway industry needs much more power than a standard passenger car and 24vDC systems are quite common. But there is only so much you can do off of a 12v or 24v system. While OEM’s are using greater than 300 amp systems, it starts getting difficult to run wire in the 3/0 AWG range so I would even say 200 amps is a reasonable cutoff.
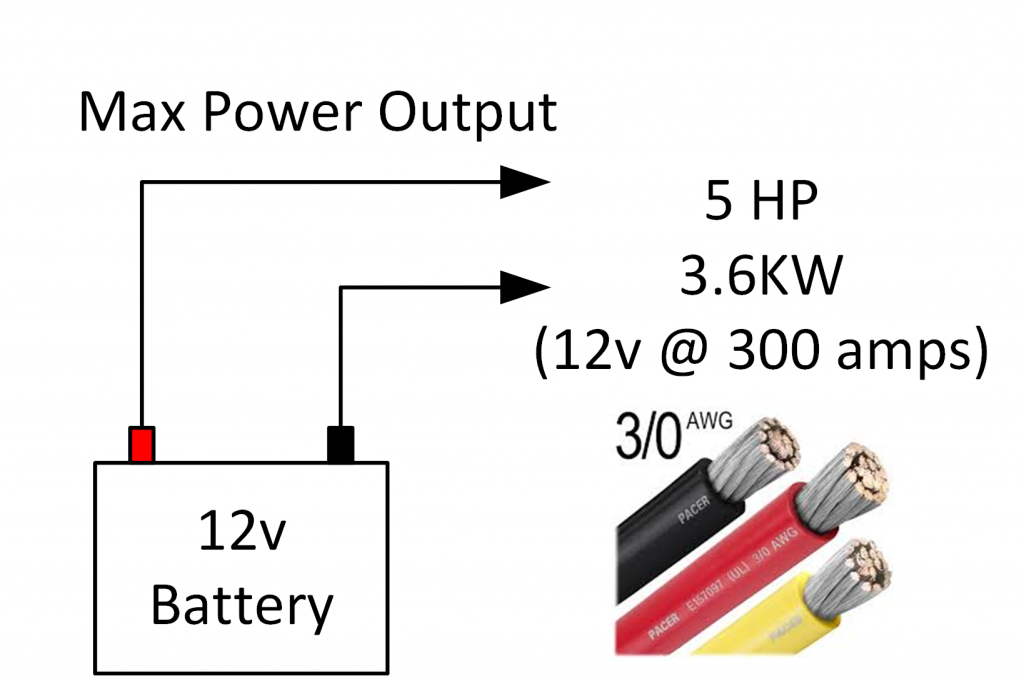
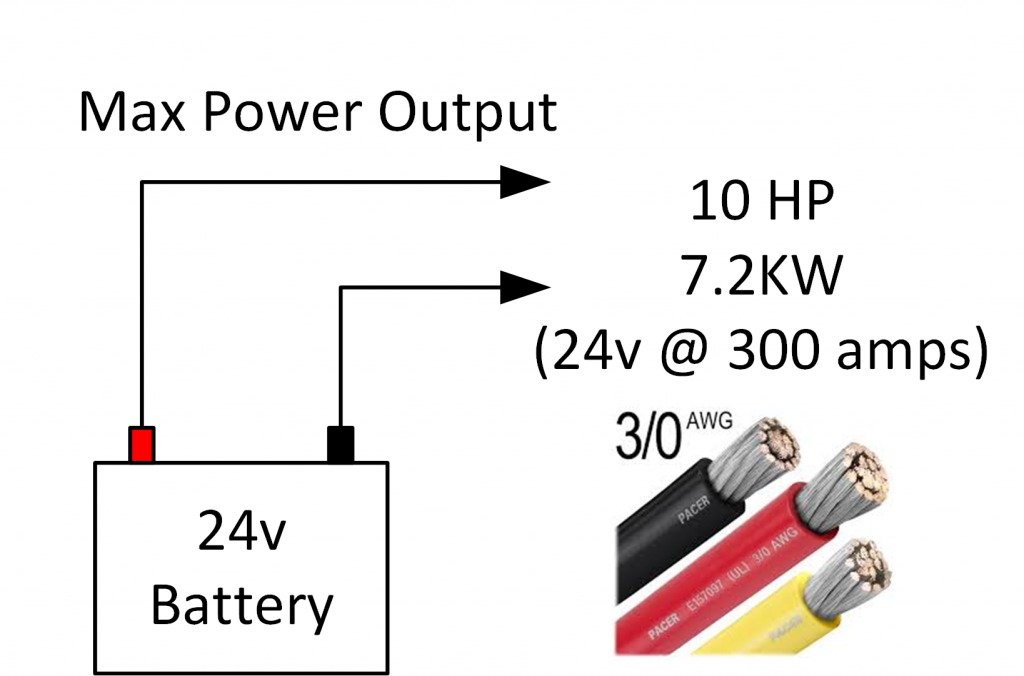
Thus, a higher voltage system is required to get the type of power needed for off-highway equipment. And once you go over 48v (this is where the voltage becomes unsafe, OSHA link HERE) you might as well go as high as practical since the safety requirement are pretty much the same.
Most high voltage systems now are rated up to about 600vDC. This is due to the rating system on many of the electrical components that are available. Electrical components are rated on the maximum voltage they can withstand and typically this comes in either 600v or 1200v ratings. There is a worldwide push to go to 1200v ratings but the components are significantly more expense and not readily available. So for the next 5-10 years, we will see the 600v systems as the standard for off-highway while the automotive industry matures the supply chain of 1200v components.
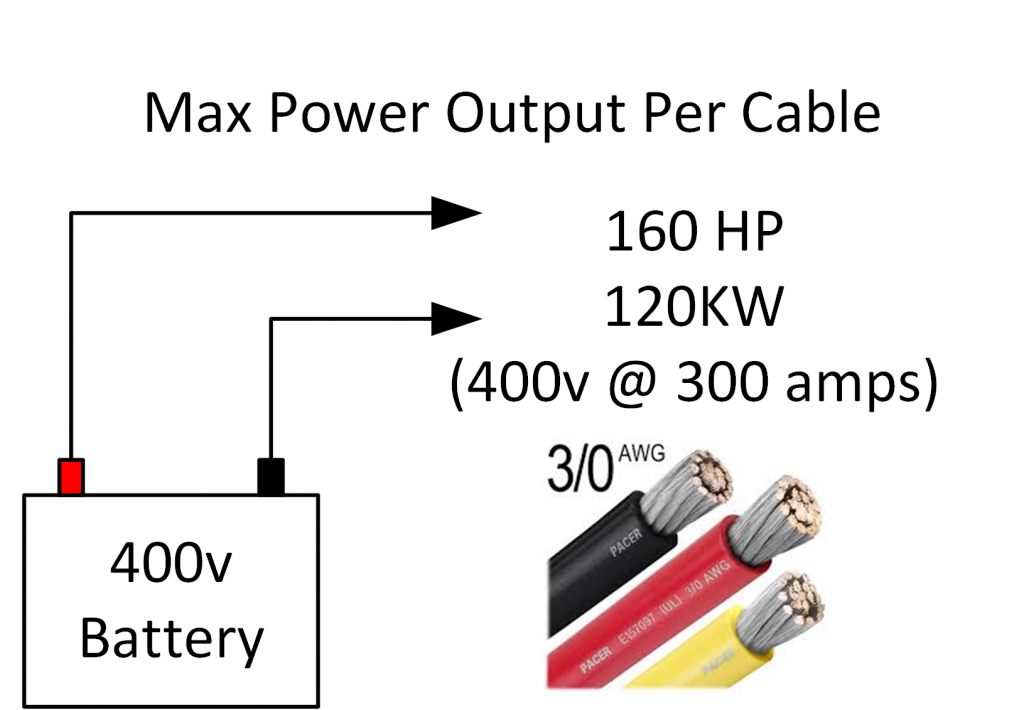
Now you can get 160 HP out of the same 300 amp cable which will power a large percentage of the heavy equipment out there. Since you can run multiple circuits off of a high voltage battery, you can now begin to design a system to run the heavy-duty, off-highway vehicles we work with every day.
But there is one major problem to implementing this type of system……
All of the vehicle systems such as lights, motors, fans, pumps, sensors, radios, valve solenoids, etc, etc, are built off of a 12v electrical architecture. So how do you run all of these components now? Simple, just step the 400vdc down to 12vdc right? Well here is where it becomes complex. First off, there are just not that many manufacturers of DC/DC converters so you need to first find out what is out there. Then the following problems quickly arise:
- How do I size the DC/DC converter?
- How do I install protection for the converter?
- How do I liquid cool the converter?
- How do I control the converter?
- How do I mount the converter?
- What is an HVIL connector and where do I get one?
- What is a pre-charge system to protect the converter and where do I get one?
- What are the standards for high voltage wiring to the converter?
- What types of certifications are needed for high voltage wiring to the converter?
- What if I need 12v plus 24v for different components?
- ……… 405. OMG that converter is expensive!